Challenges and Improvements of Wafer Dicing
- ameliasmith6520
- Aug 18, 2022
- 3 min read
Wafer dicing is a process used in semiconductor manufacturing to separate the die and wafer. It can be done in several ways including mechanical sawing, laser cutting, or scribing and breaking. Read on to learn more about the process and what can be done to improve it. Listed below are some of the challenges and improvements of this process. And don't forget to share your thoughts and experience about wafer dicing
Process of cutting a silicon wafer into individual components
There are two main methods used for cutting a silicon wafer into individual components. The first is through-cutting, which involves cutting the wafer with a single blade. The second method is referred to as step-cutting and involves cutting the wafer in two passes with blades of varying thicknesses. On the first pass, the first blade will cut through the device layers, exposing the bulk silicon. On the second pass, the other blade will cut through the remaining silicon.
The next step in cutting a silicon wafer involves applying a dopant. Dopants are elements from Groups 3 and 4 of the periodic table. These elements change the properties of the material to allow certain semiconductors to conduct current and electricity. Examples of dopants are Phosphorus and Boron, which are used to produce N-type semiconductors. After the dopants are applied, the silicon wafer is ready for the next step - assembling the individual components.
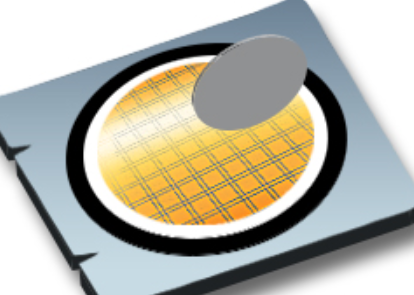
Techniques used
In the electronics industry, dicing is a common process for cutting small blocks of semiconducting material from a wafer. Some dicing methods use a laser beam to cut through the wafer. These methods may also involve wax mounting or wafer scribing. Some dicing methods also include the use of a die bonder. Wafers must be kept clean during the dicing process to avoid contamination and residual stress.
One of the most common types of dicing involves using a rotating blade. This blade crushes the material and removes debris at the same time. The blade moves along a dedicated dicing street that separates active areas of the dice. When the blade travels along these streets, it creates a groove in the substrate material. The width of the groove is proportional to the blade thickness.
Challenges faced
The challenges faced when wafer dicing include the size of the wafer, a deteriorating surface tension, and the increased exposure time to coolant. These problems can result in increased processing time, reduced yield, and even device failure. Some of the challenges faced during wafer dicing are related to the front-of-line environment for semiconductor manufacturing. The presence of static charges, such as electrostatic discharges, can negatively impact the quality of the resulting device. To overcome these challenges, semiconductor manufacturers can use specialized wafer types for this process.
The most difficult material to cut is silicon carbide, which is the third hardest substance on earth. It is ranked number 13 on the revised Mohs scale and is harder than diamonds. Silicon carbide is also very brittle, which makes cutting it with a saw blade or laser a tedious and expensive process. The same goes for reducing the size of the bond pads. However, this process does reduce water consumption by six hundred twenty-two tons a year.
Improvements possible
Improved wafer dicing processes require careful design and parameter tuning. The amount of backside chipping depends on the wafer thickness. The photos on this page show a 25 um-thick silicon wafer processed with two different blades, #2000 and #4800. The latter has finer grit and imparts less shock on the workpiece. The result is a higher yield and a higher quality package.
Plasma dicing has several advantages over traditional dicing methods. It produces fewer heat-affected zones and causes no mechanical damage. It can also produce higher break strength than laser and blade dicing, which is particularly important for dies under high stress. The non-mechanical nature of plasma dicing makes it suitable for thin-die applications. Plasma dicing can also yield higher yields than laser dicing.
Improved siC wafer dicing processes can improve cutting quality, throughput, and costs. New technologies for dicing are also being developed, including a thermal separation method. This technique is appropriate for dicing hard-brittle materials, such as SiC. In addition, the development of a theory for crack generation along a predetermined trajectory will enrich the understanding of fracture behavior in micro-nano manufacturing.
Comments