Types of Wafer Dicing
- ameliasmith6520
- Dec 7, 2022
- 3 min read
Among the most important techniques in semiconductor manufacturing are laser ablation dicing, chemical dicing and plasma dicing. Laser ablation dicing is a method of applying heat to a semiconductor wafer dicing without damaging the substrate, while chemical dicing is a process of removing an unwanted component from a semiconductor wafer. Plasma dicing is a process of cutting a semiconductor wafer using a plasma source, such as a laser, to destroy an unwanted component.
Laser ablation dicing
During laser ablation dicing, a highly concentrated laser beam is focused on a minute area for a short period of time. This process allows higher speeds for cutting and throughput. In addition, it does not generate debris that would otherwise be difficult to remove.
A new laser cut technique for semiconductor wafers is gaining attention. It involves laser-induced perforations of the wafer and tape expansion to separate the individual chips. The process also has the advantage of not generating debris, but a few technical issues remain to be addressed.
One of the key issues in laser ablation dicing is the removal of material from the kerf. The laser beam travels the length of the wafer at 300 mm/s. This speed is too high for the delicate thin wafers that are being processed.
Chemical dicing
Several types of dicing processes are used to form integrated circuit chips on a wafer. These include blade dicing, plasma dicing, and chemical dicing. They have different advantages and disadvantages. In addition, they can leave contaminant residues on the wafer. These residues can lead to corrosion and poor bonding performance.
Chemical dicing can create trenches as small as eight mm and vertical trenches as long as 150 mm. In addition, it can be used to form free-shape die. It can also decrease the size of mini-LED dies. It is safer than other dicing methods, including thermal dicing. Chemical dicing is also known for its damage-free nature.
In chemical dicing, the wafer is exposed to a solution of a chelating agent and a surfactant. The surfactant is typically a secondary alcohol ethoxylate. The solution is diluted from one tenth to one hundredth of its weight in deionized water. The solution has a pH above four.
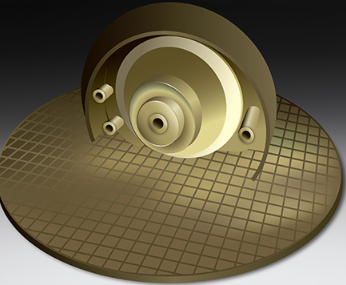
Blade dicing
Various types of dicing systems are available for wafer dicing. One type is based on abrasive grit, embedded in an electroplated nickel matrix. It is designed to provide minimal residual stress while delivering good cut quality. It is considered the least expensive solution for dicing wafers.
The dicing process requires a lot of precision and control. Uncontrolled factors include blade-to-blade variation, nozzle clogging, operator errors, and blade condition.
The process can be controlled through parameter optimization. This includes the process's feed rate, the speed of the rotating disc, the accuracy of the indexing axis, the accuracy of the cut placement, and the amount of chipping. All these parameters have an effect on the throughput. By combining them, a dicing process can be optimized to achieve optimum throughput.
Stealth dicing
Several types of dicing methods can be used to cut semiconductor wafers. Some of the most common techniques are laser ablation and blade dicing. Choosing a suitable dicing method is important to ensure the best results. This includes understanding the properties of the materials involved, and choosing a process that is tailored to the needs of the specific application.
Blade dicing is the most common technique used to cut semiconductor wafers. It uses a rotating blade made of diamond grit embedded in an electroplated nickel matrix. The blade cuts the crystal plane and divides the wafer. However, it suffers from problems with debris contamination. It also produces thermal damage.
Laser ablation dicing works in the same way, but it uses a laser beam. It pulverizes the wafer material as it cuts through it. The beam is attenuated from 100% to about 62%. It is a relatively inexpensive method.
Plasma dicing
Several techniques are employed for dicing of semiconductor wafers. The process of plasma dicing holds great promise as a non-contact process. This method is also called through-silicon-via plasma etching. In a plasma dicing process, a mask is positioned on the silicon wafer's surface and is then etched. This process provides a low temperature and a low stress process.
Plasma dicing of wafers involves the use of a thinned substrate and a custom mask. It offers good yields and overall etch quality. However, plasma dicing has some inherent disadvantages. It is difficult to integrate into backend processes, and the process is not inexpensive.
The dicing process is long. The cost per die depends on several factors. The number of die per wafer and the amount of chipping are important. The initial cost of the system and consumables are also important.
Comments